Die unterschiedlichen Oberflächenbeschichtungen bei Schrauben
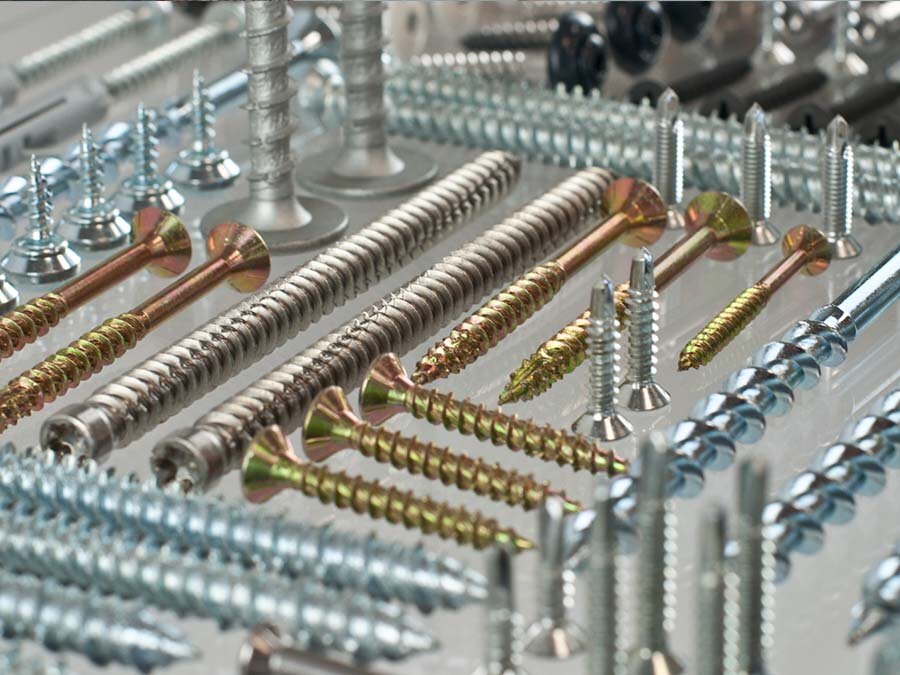
Lesezeit: 6 Minuten
Es gibt viele Arten von Schraubenbeschichtungen, die den Schutz der Verbindungselemente vor Korrosion (Oberflächen-, Rillen-, Loch- und Spaltkorrosion) gewährleisten. Je nach Anwendungsbereich werden unterschiedliche Beschichtungen verwendet. Einige dienen dem Korrosionsschutz und andere nur optischen Zwecken.
Inhalt
Warum haben Schrauben eine Beschichtung?
Der permanente Korrosionsschutz
Kopflackierte Schrauben mit Nass- oder Pulverbeschichtung
Warum haben Schrauben eine Beschichtung?
Durch eine zusätzliche Beschichtung werden hochwertige Schrauben noch effektiver. Die Schraube erhält eine dünne Schicht von nur wenigen Mikrometern. Hierdurch wird die Oberfläche der Schraube optimiert und es kann eine bessere Leistung erzielt werden. Die Beschichtung reduziert unter anderem die Reibung, wirkt optisch edler und sorgt für einen noch besseren Korrosionsschutz.
Blanker Stahl
Schrauben aus blankem Stahl haben keine Oberflächenbeschichtung. Hierdurch rosten sie schneller und nach einer Weile fängt die Schraube an zu oxidieren und wird anschließend schwarz. Neue blanke Schrauben sehen aus wie verzinkte Schrauben, mit einem etwas matteren Material. Aus diesem Grund werden die meisten Schrauben mit einer Beschichtung vorübergehend oder langfristig geschützt.
Der permanente Korrosionsschutz
Damit die Verwendung von Stahl im Außenbereich möglich ist, werden Schrauben mit einem permanenten Korrosionsschutz versehen. Dies wird durch das Aufbringen oder Entfernen von Schichten ermöglicht. Zum Aufbringen dieser Schichten gibt es viele verschiedene Optionen:
Metallische Überzüge
Als Überzugsmetall eignen sich besonders Zink, Zinn, Chrom, Nickel, Blei, Cadmium, Kupfer und natürlich die Edelmetalle, wenn der Zweck die Aufwendung dafür rechtfertigt.
Schmelzüberzüge
Feuerverzinken ist ein Schmelzprozess, wobei die Schraube in ein heißes Zinkbad bei 455 bis 480 °C getaucht und beschichtet wird. Anschließend wird die Schraube geschleudert und abgekühlt, indem man sie in Kontakt mit Wasser oder Luft bringt.
Ein weiterer Schmelzprozess ist das Aufbringen von Zinklamellenüberzügen. Für diesen Prozess wird eine Zinklamellendispersion aus Zink und Aluminiumstückchen in ein Tauchbad gegeben und anschließend eingebrannt. Je nach gewünschtem Korrosionsschutz kann der Vorgang 2- bis 3-mal wiederholt werden.
Galvanisch
Das bekannteste Verfahren ist das Galvanisieren. Hierbei wird Zink über ein Elektrolytbad auf die Schraube aufgetragen. Durch die Passivierung und eine zusätzliche Versiegelung kann der Korrosionsschutz deutlich verbessert werden. Je dicker die Beschichtung, desto höher die Korrosionsbeständigkeit. Die verzinkten Schrauben halten äußeren Einflüssen nicht nur besser stand, sondern sehen optisch auch edler aus.
Feuerverzinkt
Der Unterschied zwischen Feuerverzinkung und Verzinkung liegt in dem Verfahren. Beim Feuerverzinken wird das Befestigungselement in eine 450 °C heiße Schmelze mit flüssigem Zink getaucht und gewährleistet dadurch einen noch besseren Schutz. Für Innenbereiche oder dort, wo die Stelle weder an Wetter noch Feuchtigkeit ausgesetzt ist, sind galvanisch verzinkte Schrauben meistens ausreichend.
Gelb verchromt
Gelb verzinkte oder verchromte Schrauben sind normal verzinkte Schrauben mit verchromten Schichten, die die Korrosionsbeständigkeit noch ein wenig verbessern. Spanplattenschrauben sind oft gelb verzinkt. Es gibt aber auch gelb verzinkte Unterlegscheiben, Muttern und anderen Schrauben, welche allerdings nicht so oft verwendet werden.
Kopflackierte Schrauben mit Nass- oder Pulverbeschichtung
Wer für die farbige Fassade die passenden Schrauben benötigt, kann auf eine Nass- oder Pulverbeschichtung zurückgreifen. Eine Kopflackierung dient zu mehrere Zwecken. Sie verleiht der Schraube eine dekorative Farbe, gleicht die Farbe an die Verbindungsstelle an und bietet Korrosionsschutz. Normalerweise reicht eine Lackierung am Schraubenkopf völlig aus, da nach dem Einschrauben das Gewinde nicht mehr sichtbar ist.
Wenn jedoch der Korrosionsschutz gewährleistet werden soll, ist es sinnvoll, die gesamte Schraube zu lackieren. Bei Verwendung von Pulverlack wird der Lack elektrostatisch auf das leitfähige Material gesprüht und anschließend bei 180 bis 200 °C eingebrannt. Hierdurch erhält die Schraube eine besonders harte Schicht mit hoher Schlag-, Abrieb- und Kratzfestigkeit. In der Vergangenheit war die Farbauswahl von Pulverlacken begrenzt, inzwischen steht eine Vielzahl von Farben zur Auswahl.
Phosphatiert
Die Phosphatierung wird z. B. bei Schnellbauschrauben verwendet. Durch eine chemische Reaktion zwischen der Metalloberfläche und der wässrigen Phosphatlösung wird eine fest gebundene Umwandlungsschicht aus Metallphosphat gebildet, um Korrosion zu verhindern. Aus Umweltschutzsicht ist diese Methode nicht optimal, da Schlamm und Abwasser als gefährlicher Sonderabfall entstehen.
Edelstahl
Edelstahl ist teurer als verzinkter Stahl und wird in Bereichen mit hohen Hygieneanforderungen, wie Labors oder Restaurants eingesetzt. Dank dieser Legierung haben Edelstahlprodukte eine längere Lebensdauer als verzinkter Stahl. Wenn die Zinkschicht mit der Zeit abnimmt, verliert der Stahl seine Korrosionsbeständigkeit. Edelstahl kann seine Leistung jedoch über viele Jahre ohne Nachbesserung beibehalten.
➔ In unserem Shop finden Sie eine große Auswahl an Edelstahlschrauben.